Reducing, reusing, recycling in vehicle construction
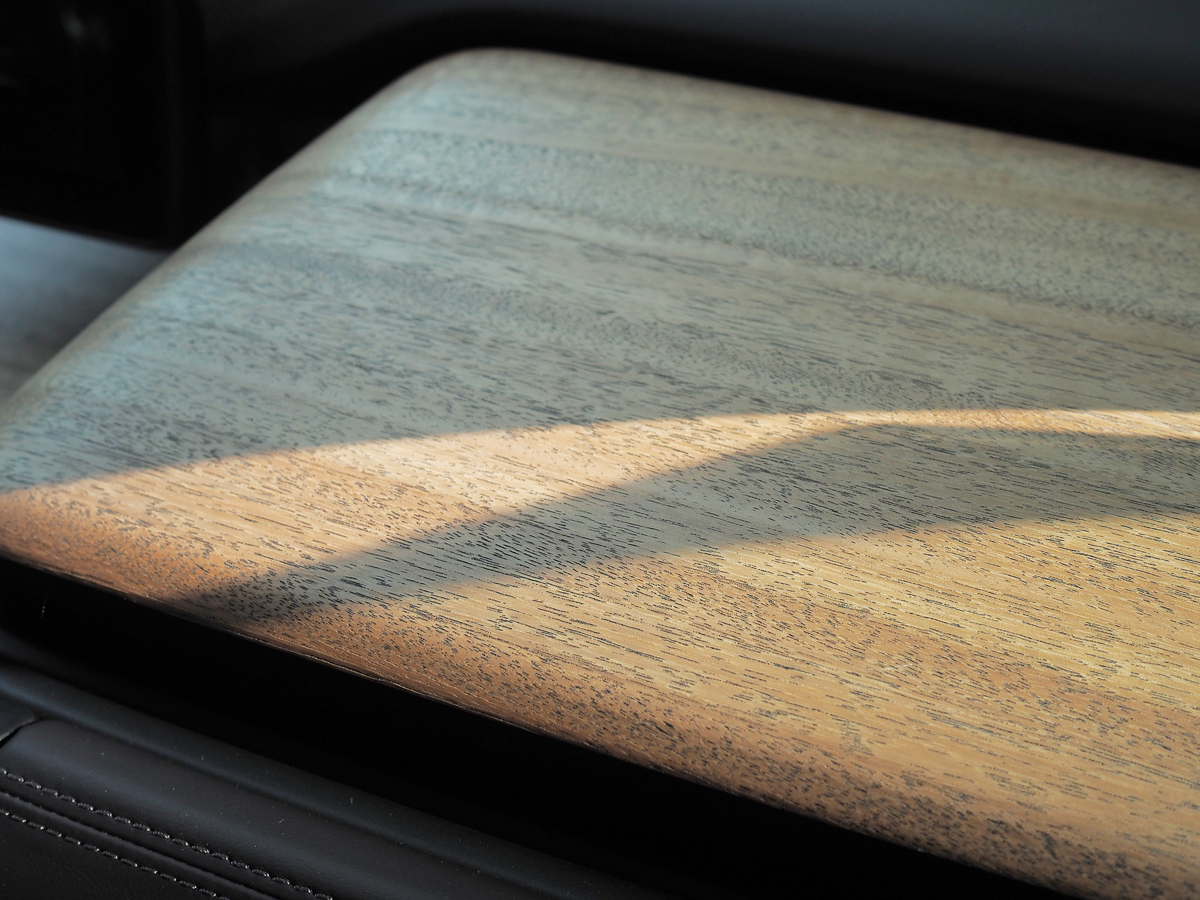

Whether it’s corn-based cutlery you find in your takeout bag or the reusable coffee cups they sell for a dollar at Starbucks, its clear businesses are trying to be more sustainable nowadays. This is by no means restricted the food industry, as we’re increasingly hearing more about automotive manufacturers using recycled components in vehicle construction.
In fact, every time we go for a drive we may very well be interacting with several recycled parts. Jaguar Land Rover (JLR) and BMW are two automakers that have fully embraced this philosophy of replacing scarce or synthetic materials with environmentally friendlier options.
Many car companies tout their widespread use of aluminum and how it makes their products lighter and more responsive. But JLR talks about the green benefits — working with the REAL CAR initiative, a method has been devised where scrap aluminum taken from presses is re-melted and combined with high-grade sheet metal alloy. An example of a model that utilizes this technique is the Jaguar XJ sedan.
JLR is also experimenting with implementing a closed loop waste recovery and recycling system at two production facilities where the all-aluminum Range Rover and Range Rover Sport are built.
For BMW, The luxury German brand’s story really begins with the launch of the “sustainable mobility” i division cars, namely the i3 pure-electric hatchback and the i8 hybrid sports car released in 2013 and 2014, respectively. According to i program manager Marc Belcourt, nothing about these vehicles are similar to anything else made by the Munich-based company.
“When it came to this car, we didn’t just tap into the existing production line in Leipzig (Germany). We built an entire new production facility, which is powered by wind turbines. You can see these massive turbines right outside the plant, generating renewable energy to make the i3 and the i8,” said Belcourt.
Part of the reasoning behind setting up a fresh facility is simply that a lot of the materials used in construction are entirely different. One glance in the interior of the i3 and that becomes immediately clear. For instance, parts of the dash and trim panels on the door look almost like carpeting — that’s made from fibres from a plant known as kenaf. On i3s with the cloth seats, the covers are derived from 100 per cent recycled polyester, manufactured from up to 34 per cent PET (polyethylene terephthalate). By weight, 25 per cent of the plastics used in the in the cabin are recycled.
Besides utilizing reconstituted ingredients, the wood that you see in the car is sourced from eucalyptus trees farmed in certified European plantations, and any leather used is tanned with a natural process using extract from olive leaves.
“More and more people are seeing sustainability as a trend that they would like to be a part of and they would like to associate with,” says Belcourt. “People’s values are changing.”